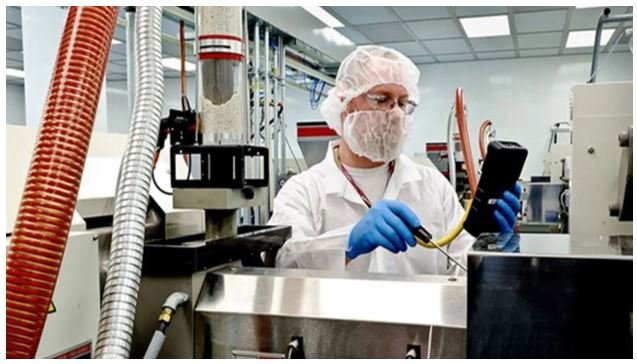
ISO 13485 Medical Devices Quality Management Systems
Guidance Consulting and Training provides qualification, training, and grant services for the international standard (ISO 13485) for quality management for medical device manufacturers in Saudi Arabia, as the requirements of this standard are specified for quality management of medical device manufacturing. This system aims to demonstrate the enterprise’s ability to provide medical devices and related services of high quality that meet the requirements of the customer and relevant regulatory bodies.
This standard provides support and guidance to manufacturing institutions to ensure the application of international quality standards in the design, development, manufacture, and distribution of medical devices to ensure the safety and effectiveness of these devices and maintain customer satisfaction. It also intends to ensure that manufactured medical devices meet the specified quality and safety requirements and provide customer trust in the provided products and services.
The Importance of Implementing ISO 13485 in Saudi Arabia
ISO 13485 improves the operational processes of companies specialized in manufacturing and supplying medical devices. The following is the importance of implementing this system in healthcare:
- ISO 13485 improves the reliability and safety of manufactured medical products. By complying with this system, organizations can ensure that quality and safety requirements are met, thus providing safe medical products to consumers.
- The system improves companies’ operational processes, allowing for increased efficiency and reduced errors in the manufacturing process. This means that medical products manufactured according to ISO 13485 will be more accurate and of higher quality.
- ISO 13485 is committed to matching globally recognized best practices in the medical device industry. Therefore, adherence to this system will help organizations comply with strict laws and regulations related to health, safety, and quality in healthcare.
- The system specifies the requirements that must be met by medical device manufacturers. Compliance with ISO 13485 is a prerequisite for accessing most global markets. Therefore, implementing this system allows companies to expand and grow in the international medical devices market.
- Compliance with ISO 13485 standards is a clear indication of a commitment to quality, safety, and superior professional practices in the medical devices industry. Consequently, this system enhances the organization’s reputation and increases customer confidence in its products.
ISO 13485:2016 Requirements
A quality management system that complies with ISO 13485:2016 is essential for medical device manufacturers and suppliers.
Scope: This point defines the scope of application of the medical devices quality management system within the organization.
Normative references: This point contains a list of normative references in which the implemented system must participate.
Terms and definitions: This point explains the basic terms and definitions used in the system.
Quality management system: How to build and implement a quality management system based on ISO 13485. It also requires the availability of documents and records to prevent things that may negatively affect the quality of medical devices.
Management responsibilities: The top management in the organization is responsible for implementing the quality management system and ensuring compliance with the standard.
Resource management: Includes requirements for allocating the resources necessary to implement and maintain the quality management system.
Product realization: Describes the procedures necessary to implement medical devices manufacturing and supply process and ensure compliance with the standard.
Measurement analysis and improvement: Addresses the measures that must be taken to measure the performance of the quality management system and analyzes the collected data to improve performance continuously.
Benefits of ISO 13485 Medical Devices Quality Management System
- Enable access to international markets that require certification such as Canada and Europe.
- Reduce operational costs by highlighting deficiencies in processes and improving their efficiency and effectiveness.
- Enhance product safety and quality and provide greater confidence to consumers.
- Develop reliable and documented procedures that comply with industry standards.
- Demonstrate commitment to quality through an internationally recognized standard.
- Increase customer satisfaction by providing high-quality products and regularly handling complaints.
- Add transparency to how complaints, monitoring, or product recalls are handled.
- Implementing a quality management system generally helps motivate employees and provides a better definition of key roles and responsibilities.
Improve operational efficiency and ensure compliance with international quality standards for any organization specializing in the medical device industry by implementing a quality management system compatible with ISO 13485:2016. Implementing a quality management system for medical devices in manufacturing organizations is crucial to maintaining high quality and safety in manufacturing various medical devices. Therefore, implementing this system in an effective manner proceeds according to these steps:
Step 1: Identifying regulatory requirements
By understanding and identifying all relevant regulatory requirements for the medical device industry reviewing local and international laws and regulations related to this type of product and ensuring that they are applied correctly.
Step 2: Risk Management
Identify and evaluate all potential risks that may affect the quality of medical products and public safety, and then develop and implement strategies to deal with these risks and reduce them to a minimum.
Step 3: Supplier Controls
Develop accurate procedures and controls to identify and evaluate potential suppliers choose the best among them, and ensure that all contracts and agreements are documented and that suppliers comply with health standards and laws specific to the industry.
Step 4: Determine the design, manufacturing, and production processes
Define and document all design, manufacturing, and production processes for medical devices. Ensure all steps and procedures are clearly defined, detailed, and consistent with applicable regulatory requirements and quality standards.
Step 5: Implementing the Quality Management System
After completing the definition and documentation of all the previous steps, you must implement the quality management system fully and effectively. All employees in the organization must be familiar with this system and apply it in their daily work. Additionally, the necessary training must be provided to employees, and the implementation of the system must be monitored continuously to ensure full compliance.
Recent updates to the ISO 13485 medical devices quality management system.
The recent updates include many important aspects, such as improving evaluation and review procedures and identifying risks related to medical devices. They also focus on improving medical devices’ safety and sustainable performance, emphasizing supply chain management and accurate and continuous monitoring of manufacturing processes. Implementing these updates aims to ensure that medical devices comply with safety and quality requirements, thus ensuring patients’ highest level of healthcare.
ISO 13485 vs. ISO 9001
While both standards focus on the quality management system, there are some key differences between them.
- ISO 9001 is more general and can be adopted by any organization, while ISO 13485 is specific to medical devices and related services.
- The new version of 9001 is more risk-based, while the older versions were process-based. On the other hand, 13485 has always been risk-based.
- Some additional clauses in 13485 were absent in 9001, such as design, development, sterilization, and software validation for medical devices.
- ISO 9001 certification is not mandatory in most countries but ISO 13483 certification is a must in European countries.
Compatibility with ISO 9001:2008 and not ISO 9001:2015
ISO 13485 complies with the requirements of ISO 9001:2008 and not ISO 9001:2015. This incompatibility is because the amendments to both standards were completed in parallel and because ISO 9001:2015 was deemed unnecessary for medical devices. These changes were managed by an ISO 210 technical committee, whose task was to ensure this standard kept the quality management system fit for its intended purpose.
What are the main requirements for obtaining ISO 13485 certification?
To obtain ISO 13485 certification, medical device manufacturers must meet the following set of main requirements:
- Establish a medical device quality management system: Manufacturers must establish a quality management system based on ISO 13485. This system aims to organize and manage all quality aspects of the medical devices industry.
- Implement regulatory requirements: Companies must demonstrate the ability to meet regulatory requirements applicable to medical device services. These requirements include relevant local and international laws, regulations, and standards.
- Devices: Companies must demonstrate their ability to provide high-quality medical devices and follow approved health requirements and standards.
- Commitment to customer requirements: Companies must consistently meet customers’ requirements by the specified standards and specifications.
- Provide technical documents: Companies must provide a set of technical documents required to ensure the quality of their products and compliance with health standards.
- System Review: The company’s system must be reviewed and evaluated periodically to ensure compliance with ISO 13485 standards.
- Request for Certification: After completing all the necessary stages and implementing the system, the company must apply for ISO 13485 certification from an accredited certification body.
Guidance Consulting and Training Company has the necessary competencies and experience to help institutions and individuals implement international specifications, improve business, and ensure compliance with the requirements of legislative and regulatory bodies. Contact us now to benefit from the expertise of our specialized consultants.